GARAGE OR CAR PARK FLOORS
To know which type of paving is the most appropriate for your garage, we have to analyse its condition to be able to offer the best solution.
Paving for garages should fulfil a series of requirements:
It has to be resistant to abrasion, collisions and chemical agents, dustproof, non-slip and waterproof
PROCESS
1st) Preparation of the base (grit blasting, diamond polishing, milling, sanding)
2nd) Meshing of joints and cracks
3rd) Repair of damage
4th) Application of the first layer of resin
5th) Application of the quartz powder
6th) Superficial sanding
7th) Application of the third layer of resin
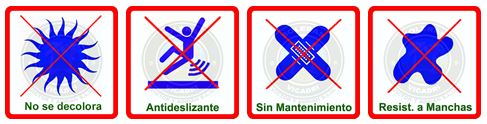
Description of the Process
1st) Preparation of the base:
This is one of the most important steps of the process, having an adequate base is the key to having a good result in paving. To achieve this once the base has been inspected we should choose the best way to prepare it. There are different preparation methods (mechanical or chemical cleaning).
Mechanical cleaning
Grit blasting: blasting using metal balls and then there collection.
Diamond polishing, sanding and preparation of the existing base.
Milling: grating of the base by means of steel blades and collection of the debris.
Sanding: sanding by means of carborundum discs or diamond sanders.
Chemical cleaning: thorough degreasing and then the use of chemicals to open the pores of the base material.
2nd) Repair of joints and cracks:
This is the process of repairing the existing joints in the paving and the cracks that could have been caused by the movement of the base (retraction). This treatment is done using a quick drying epoxy resin bicomponent product and applying quartz to the joint or crack being repaired. The application of the resin is done using a metallic trowel. Before having applied the resin the joints and crack will have been regularised by using an angle grinder.
3rd) Repair of damage
Possible damage to the base like holes and chips can be repaired by using the three components of the mortar: the epoxy resin, the catalyser and finally silicon dioxide aggregate of different selected granulometry, which will be selected depending on the type of defect to be repaired. The application of the mortar will be done by using a grouting tool and if needed can be altered until level with the ground.
4th) Application of the first layer of resin
The product applied is a reticulated epoxy resin with an amine reagent, which varies according to the temperature that we have at the time of application (slow in summer and fast in winter). Once the two components have been mixed we incorporate into the resin a mixture of aggregates (fine, medium and coarse) with the aim of having the adequate thickness of resin when applied using the trowel. Once the resin has been applied it is covered by medium sized aggregate until a thickness of 1.5 – 2 mm has been obtained. The drying time varies with temperature but we should estimate an average time of 4 hours. Once the layer is dry the excess aggregate can be removed.
5th) Application of the second layer of resin
The method of application, consumption and characteristics are the same as in the previous step. We should bear in mind that at the moment we cover the resin with the aggregate it should be fully covered because at this point we differentiate between multi-layers of single colour and multicolour. In the case of a single colour the aggregate (natural) is granulometric but with a colour treatment based on polyurethane.
6th) Superficial sanding
Once the two layers of resin have been applied and the excess aggregate removed, the surface is sanded using carborundum discs until we get the degree of roughness desired.
7th) Application of the third layer of resin
In the case of a multilayer single colour finish the product would be a defined RAL colour and in the case of a multilayer multicolour finish will be applied using a rubber spatula.
Once this layer has been applied the paving is finished, the hardening time for pedestrian use is 24 hours, for vehicle use is 48 hours and maximum strength is reached 6 days after application.
This is the standard process, depending on the paving and needs of the client this process can be modified but always under the supervision of our technical staff.
We have various systems from epoxy resin paints, polyurethane, methacrylate, etc.
Where we can install it: Transport buildings: garages, bus stations, car parks, bus shelters, awnings, service areas and petrol stations, rest areas, airport terminals, control towers, heliports and hangers.